Продукциянын эксплуатациялык касиеттерин баалоо жана материалдардын физикалык-механикалык мүнөздөмөлөрүн аныктоо үчүн ар кандай инструкциялар, ГОСТтор жана башка ченемдик-кеңеш берүүчү документтер колдонулат. Продукциянын бүтүндөй сериясын же бир эле түрдөгү материалдын үлгүлөрүн жок кылууну сыноо методдору да сунушталат. Бул өтө үнөмдүү ыкма эмес, бирок натыйжалуу.
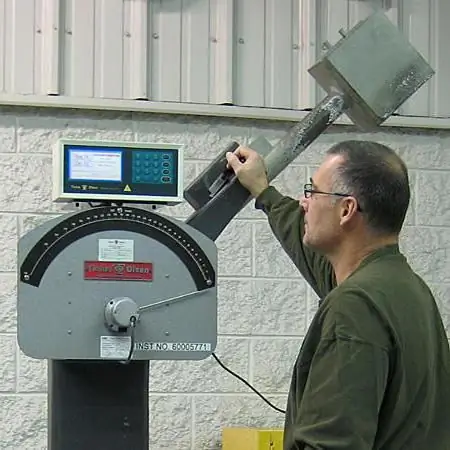
Мүнөздөмөлөрдүн аныктамасы
Материалдардын механикалык касиеттеринин негизги мүнөздөмөлөрү төмөнкүдөй.
1. Соруу күчү же тартылуу күчү - үлгү жок кылынганга чейин эң чоң жүктө белгиленген стресс күчү. Материалдардын бышыктыгынын жана пластикасынын механикалык мүнөздөмөлөрү катуу заттардын сырткы жүктөрдүн таасири астында форманын кайтарылгыс өзгөрүшүнө жана бузулуусуна каршы туруу үчүн касиеттерин сүрөттөйт.
2. Шарттуу кирешелүүлүк - бул калдык штамм үлгү узундугунун 0,2% жеткендеги стресс. Булэң аз стресс, ал эми үлгү стресстин байкаларлык көбөйүүсүз деформациясын улантууда.
3. Узак мөөнөттүү күчтүн чеги белгилүү бир температурада үлгүнүн бузулушуна алып келген эң чоң стресс деп аталат. Материалдардын механикалык мүнөздөмөлөрүн аныктоодо узак мөөнөттүү бекемдиктин акыркы бирдиктерине басым жасалат - кыйроо 7000 градус Цельсийде 100 саатта болот.
4. Шарттуу сүрүлүү чеги - бул берилген температурада үлгүдөгү белгилүү бир убакытта берилген узартуу, ошондой эле сойлоо ылдамдыгы пайда кылган чыңалуу. Чек - 7000 градус Цельсийде 100 саат бою металлдын 0,2% деформациясы. Соймо - металлдардын туруктуу жүктөө жана жогорку температурада узак убакытка чейин деформациясынын белгилүү ылдамдыгы. Жылуулукка туруктуулук - бул материалдын сынууга жана сойлоого туруктуулугу.
5. Чарчоо чеги - чарчоо бузулбаганда цикл стрессинин эң жогорку мааниси. Жүктөө циклдарынын саны материалдардын механикалык сыноосу кандайча пландаштырылганына жараша берилиши мүмкүн. Механикалык мүнөздөмөлөргө материалдын чарчоо жана чыдамкайлык кирет. Циклдеги жүктөрдүн таасири астында бузулуулар топтолуп, жаракалар пайда болуп, кыйроого алып келет. Бул чарчоо. Ал эми чарчоого каршылык касиети - чыдамкайлык.
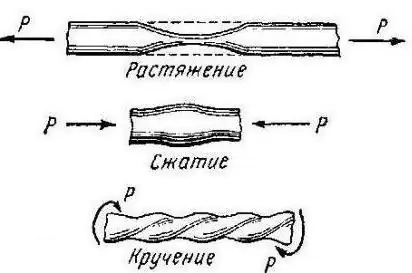
Козу жана кичирейтүү
Инженердикте колдонулган материалдарпрактика эки топко бөлүнөт. Биринчиси - пластик, анын бузулушу үчүн олуттуу калдык деформациялар пайда болушу керек, экинчиси - морт, өтө кичинекей деформацияларда кыйрап. Албетте, мындай бөлүштүрүү абдан ээнбаштык, анткени ар бир материал түзүлгөн шарттарга жараша, морт жана ийкемдүү катары өзүн алып жүрүүгө болот. Бул стресс абалынын табиятына, температурага, чыңалуу ылдамдыгына жана башка факторлорго жараша болот.
Материалдардын чыңалуусундагы жана кысуудагы механикалык мүнөздөмөлөрү ийкемдүүлүк жана морттук үчүн эң сонун. Мисалы, жумшак болот чыңалууда, ал эми чоюн компрессияда сыналат. Чоюн морт, болот ийилчээк. Морттук материалдар кысуу күчкө ээ, ал эми чыңалуу деформациясы начар. Пластмасса кысуу жана чыңалуудагы материалдардын болжол менен бирдей механикалык мүнөздөмөсүнө ээ. Бирок, алардын босогосу дагы эле созулуп аныкталат. Дал ушул ыкмалар материалдардын механикалык мүнөздөмөлөрүн так аныктай алат. Тартуу жана кысуу диаграммасы бул макаланын сүрөттөрүндө көрсөтүлгөн.
Морттук жана пластикалык
Пластика жана морттук деген эмне? Биринчиси - чоң көлөмдө калдык деформацияларды кабыл алып, кулап калбоо жөндөмү. Бул касиет эң маанилүү технологиялык операциялар үчүн чечүүчү болуп саналат. Ийүү, чийүү, чийүү, штамптоо жана башка көптөгөн операциялар пластикалык касиеттерине жараша болот. Илимдүү материалдарга күйдүрүлгөн жез, жез, алюминий, жумшак болот, алтын жана ушул сыяктуулар кирет. Бир кыйла аз ийкемдүү коложана дурал. Дээрлик бардык легирленген болоттор өтө начар ийкемдүү.
Пластикалык материалдардын бышыктык мүнөздөмөлөрү ылдыйда карала турган агымдуулуктун күчү менен салыштырылат. Морттуулуктун жана пластикалык касиеттерге температура жана жүктөө ылдамдыгы чоң таасирин тийгизет. Тез чыңалуу материалды морт кылат, ал эми жай чыңалуу аны ийкемдүү кылат. Мисалы, айнек морт материал, бирок температура нормалдуу болсо, башкача айтканда, пластикалык касиетин көрсөтсө, ал узак жүккө туруштук бере алат. Ал эми жумшак болот ийкемдүү, бирок шок жүктө ал морт материал катары көрүнөт.
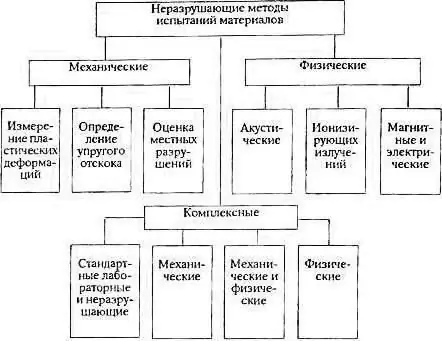
Вариация ыкмасы
Материалдардын физикалык-механикалык мүнөздөмөлөрү узунунан, ийилген, буралмаланган жана башка, андан да татаал титирөө түрлөрүнүн дүүлүгүүсү менен, ал эми үлгүлөрдүн өлчөмүнө, формаларына, кабыл алгычтын жана дүүлүктүргүчтүн түрлөрүнө, методдоруна жараша аныкталат. бекитүү жана динамикалык жүктөрдү колдонуу схемалары. Эгерде жүктү берүү, термелүүлөрдү дүүлүктүрүү жана аларды каттоо методдорунда колдонуу ыкмасы олуттуу өзгөрсө, ири өлчөмдөгү буюмдар да ушул ыкманы колдонуу менен сыноодон өткөрүлөт. Ушул эле ыкма ири өлчөмдөгү конструкциялардын катуулугун баалоо зарыл болгондо материалдардын механикалык мүнөздөмөлөрүн аныктоо үчүн колдонулат. Бирок бул ыкма буюмдун материалдык мүнөздөмөлөрүн жергиликтүү аныктоо үчүн колдонулбайт. Техниканын практикалык колдонулушу геометриялык өлчөмдөр жана тыгыздык белгилүү болгондо, буюмду таянычтарга бекитүү мүмкүн болгондо гана мүмкүн болот.продукт - конвертерлер, белгилүү бир температура шарттары керек ж.б.
Мисалы, температуралык режимдерди өзгөртүүдө тигил же бул өзгөрүү болот, ысыганда материалдардын механикалык мүнөздөмөлөрү башкача болот. Бул шарттарда дээрлик бардык органдар кеңейет, бул алардын түзүлүшүнө таасирин тийгизет. Ар бир орган курамына кирген материалдардын белгилүү бир механикалык мүнөздөмөлөрүнө ээ. Эгерде бул белгилер бардык багытта өзгөрбөсө жана ошол эле бойдон калса, мындай дене изотроптук деп аталат. Материалдардын физикалык жана механикалык мүнөздөмөлөрү өзгөрсө - анизотроптук. Акыркы дээрлик бардык материалдардын мүнөздүү өзгөчөлүгү болуп саналат, жөн гана башка өлчөмдө. Бирок, мисалы, болоттор бар, анда анизотропия өтө анча маанилүү эмес. Бул жыгач сыяктуу табигый материалдарда айкын көрүнүп турат. Өндүрүш шарттарында материалдардын механикалык мүнөздөмөлөрү сапатты көзөмөлдөө аркылуу аныкталат, мында ар кандай ГОСТтар колдонулат. Сыноонун натыйжалары жалпыланганда статистикалык иштетүүдөн гетерогендүүлүктүн баасы алынат. Үлгүлөр көп болушу керек жана белгилүү бир дизайндан кесилиши керек. Технологиялык мүнөздөмөлөрдү алуунун бул ыкмасы абдан оор деп эсептелет.
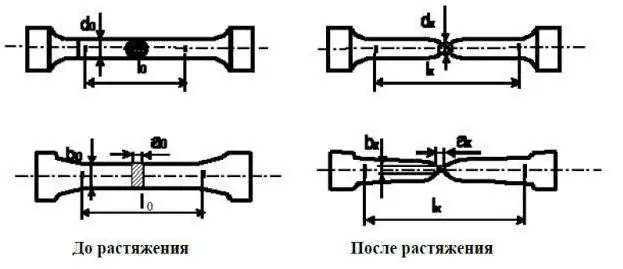
Акустикалык ыкма
Материалдардын механикалык касиеттерин жана алардын мүнөздөмөлөрүн аныктоонун көптөгөн акустикалык ыкмалары бар жана алардын бардыгы синусоидалдык жана импульстук режимдердеги термелүүлөрдү киргизүү, кабыл алуу жана каттоо жолдору боюнча айырмаланат. Акустикалык методдор, мисалы, курулуш материалдарын, алардын калыңдыгын жана чыңалуу абалын изилдөөдө, кемчиликтерди аныктоодо колдонулат. Конструкциялык материалдардын механикалык мүнөздөмөлөрү да акустикалык ыкмалар менен аныкталат. Эластикалык толкундарды, алардын таралуу параметрлерин синусоидалдык жана импульстук режимдерде жазууга мүмкүндүк берүүчү көптөгөн түрдүү электрондук акустикалык приборлор иштелип чыгып, массалык түрдө чыгарылууда. Алардын негизинде материалдардын бекемдигинин механикалык мүнөздөмөлөрү аныкталат. Эгерде аз интенсивдүүлүктөгү ийкемдүү термелүүлөр колдонулса, бул ыкма таптакыр коопсуз болуп калат.
Акустикалык ыкманын кемчилиги - бул дайыма эле мүмкүн боло бербеген акустикалык контакттын зарылдыгы. Ошондуктан материалдардын бышыктыгынын механикалык мүнөздөмөлөрүн тез арада алуу зарыл болсо, бул иштер анча өндүрүмдүү эмес. Натыйжага беттин абалы, изилденип жаткан буюмдун геометриялык фигуралары жана өлчөмдөрү, ошондой эле сыноолор жүргүзүлүп жаткан чөйрө чоң таасирин тийгизет. Бул кыйынчылыктарды жеңүү үчүн, конкреттүү бир маселени катуу аныкталган акустикалык ыкма менен чечүү керек же, тескерисинче, алардын бир нечесин дароо колдонуу керек, ал конкреттүү кырдаалга жараша болот. Мисалы, айнек стекловолок мындай изилдөөгө жакшы жардам берет, анткени ийкемдүү толкундардын таралуу ылдамдыгы жакшы, демек, кабыл алгыч жана эмитент үлгүнүн карама-каршы беттеринде жайгашкан учурда учу-кыйырсыз үндү кеңири колдонулат.
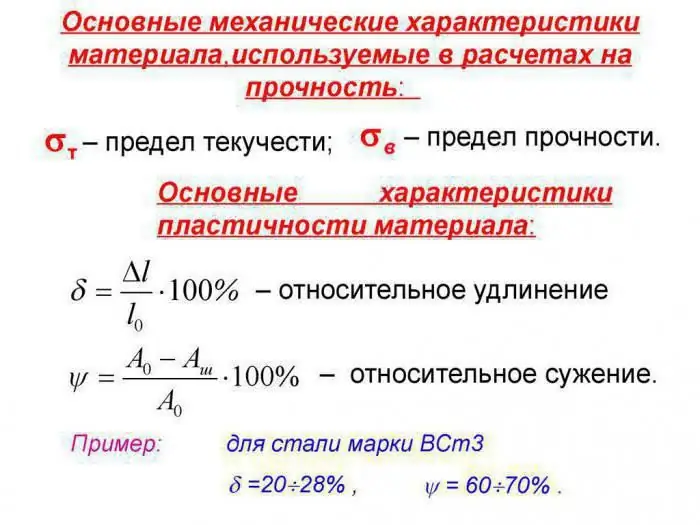
Дефектоскопия
Дефектоскопия ыкмалары ар кандай тармактарда материалдардын сапатын көзөмөлдөө үчүн колдонулат. Кыйратуучу жана кыйратуучу ыкмалары бар. Кыйратпаганга төмөнкүлөр кирет.
1. Магниттик кемчиликтерди аныктоо беттик жаракаларды жана кирүүнүн жоктугун аныктоо үчүн колдонулат. Мындай кемчиликтери бар аянттар ээн талаалар менен мүнөздөлөт. Сиз аларды атайын аппараттардын жардамы менен аныктай аласыз же жөн гана бүткүл бетине магниттик порошок катмарын сүйкөй аласыз. Кемчилиги бар жерлерде порошок колдонулганда да өзгөрөт.
2. Дефектоскопия да УЗИ жардамы менен жүргүзүлөт. Үлгүнүн тереңинде кандайдыр бир үзгүлтүктөр болсо дагы, багыттуу нур башкача чагылдырылат (чачырылат).
3. Материалдагы кемчиликтер ар кандай тыгыздыктагы чөйрөнүн нурлануу жутулушунун айырмасына негизделген изилдөөнүн радиациялык ыкмасы менен жакшы көрсөтүлөт. Гамма кемчиликтерин аныктоо жана рентген нурлары колдонулат.
4. Химиялык кемчиликтерди аныктоо. Эгерде бети азот кислотасынын, туз кислотасынын начар эритмеси же алардын аралашмасы (aqua regia) менен чийилсе, анда кемчиликтер бар жерлерде кара тилке түрүндөгү тор пайда болот. Сиз күкүрт издерин алып салуу ыкмасын колдоно аласыз. Материал бир тектүү эмес жерлерде күкүрт түсүн өзгөртүшү керек.
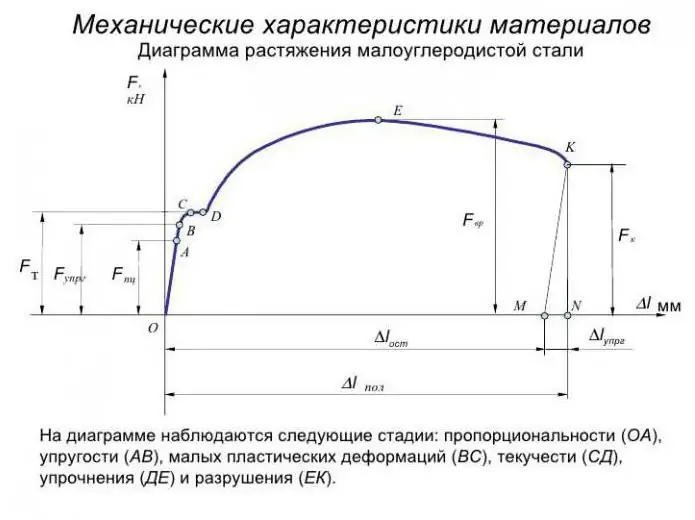
Кыйратуучу ыкмалар
Кыйратуучу ыкмалар бул жерде жарым-жартылай демонтаждалган. Үлгүлөр ийилүү, кысуу, чыңалуу боюнча текшерилет, башкача айтканда, статикалык кыйратуучу ыкмалар колдонулат. Эгерде продукттаасир ийилүүсү боюнча өзгөрүлмө циклдик жүктөр менен сыналат - динамикалык касиеттери аныкталат. Макроскопиялык ыкмалар материалдын түзүлүшүнүн жалпы сүрөтүн жана чоң көлөмдө тартат. Мындай изилдөө үчүн атайын жылмаланган үлгүлөр талап кылынат, алар оюудан өткөрүлөт. Ошентип, дандардын формасын жана жайгашуусун, мисалы, болотто, эритмеде деформациясы бар кристаллдардын, жипчелердин, кабыктардын, көбүктөрдүн, жаракалардын жана башка эритмелердин бир тексиздигин аныктоого болот.
Микроскопиялык методдор микроструктураны изилдеп, эң кичинекей кемчиликтерди ачат. Үлгүлөр алдын ала майдаланып, жылмаланып, андан кийин ошол эле жол менен оюлат. Андан аркы тестирлөө электрдик жана оптикалык микроскопторду жана рентген нурларынын дифракциялык анализин колдонууну камтыйт. Бул ыкманын негизин заттын атомдору чачыраткан нурлардын интерференциясы түзөт. Материалдын мүнөздөмөлөрү рентген нурларынын дифракциялык схемасын талдоо жолу менен көзөмөлдөнөт. Материалдардын механикалык мүнөздөмөлөрү алардын бекемдигин аныктайт, бул курулуш конструкциялары үчүн негизги нерсе, алар ишенимдүү жана коопсуз эксплуатацияда. Ошондуктан материал жогорку деңгээлдеги механикалык мүнөздөмөлөрүн жоготпостон кабыл ала турган бардык шарттарда кылдат жана ар кандай ыкмалар менен сыналат.
Контролдоо ыкмалары
Материалдардын мүнөздөмөлөрүн кыйратпай текшерүү үчүн эффективдүү ыкмаларды туура тандоо чоң мааниге ээ. Бул жагынан эң так жана кызыктуу болуп кемчиликтерди аныктоонун ыкмалары - дефекттик контролдоо болуп саналат. Бул жерде кемчиликтерди аныктоо ыкмаларын ишке ашыруу ыкмалары менен физикалык көрсөткүчтөрдү аныктоо ыкмаларынын ортосундагы айырмачылыктарды билүү жана түшүнүү зарыл.механикалык мүнөздөмөлөрү, анткени алар бири-биринен түп-тамырынан бери айырмаланат. Эгерде акыркылар физикалык параметрлерди көзөмөлдөөгө жана алардын материалдын механикалык мүнөздөмөлөрү менен кийинки өз ара байланышына негизделсе, анда кемчиликтерди аныктоо дефекттен чагылган же башкарылуучу чөйрө аркылуу өткөн радиацияны түз өзгөртүүгө негизделген.
Эң жакшы нерсе, албетте, комплекстүү башкаруу. Татаалдуулук оптималдуу физикалык параметрлерди аныктоодо турат, алар үлгүнүн күчүн жана башка физикалык-механикалык мүнөздөмөлөрүн аныктоо үчүн колдонулушу мүмкүн. Ошондой эле, ошол эле учурда, структуралык кемчиликтерди көзөмөлдөө үчүн каражаттардын оптималдуу комплекси иштелип чыккан жана андан кийин ишке ашырылат. Акыр-аягы, бул материалды бүтүндөй баалоо пайда болот: анын иштеши кыйратуучу эмес ыкмаларды аныктоого жардам берген бир катар параметрлер менен аныкталат.
Механикалык сыноо
Материалдардын механикалык касиеттери бул сыноолордун жардамы менен текшерилет жана бааланат. Мындай контроль түрү көп убакыт мурун пайда болгон, бирок дагы эле актуалдуулугун жогото элек. Ал тургай, заманбап жогорку технологиялык материалдар керектөөчүлөр тарабынан көп жана катуу сынга алынат. Ал эми бул текшерүүлөр кылдаттык менен жүргүзүлүшү керек экенин көрсөтүп турат. Жогоруда айтылгандай, механикалык тесттер эки түргө бөлүүгө болот: статикалык жана динамикалык. Биринчиси буюмдун же үлгүнүн буралышын, чыңалуусун, кысуусун, ийилишин, ал эми экинчиси катуулугун жана соккунун күчүн текшерет. Заманбап жабдуулар бул өтө жөнөкөй эмес процедураларды жогорку сапатта аткарууга жана бардык операциялык көйгөйлөрдү аныктоого жардам берет.бул материалдын касиеттери.
Чыңалууну текшерүү материалдын колдонулган туруктуу же күчөгөн чыңалуунун таасирине туруктуулугун көрсөтө алат. Метод эски, сыналган жана түшүнүктүү, абдан узак убакыт бою колдонулат жана дагы эле кеңири колдонулат. Үлгү тестирлөөчү машинадагы арматуранын жардамы менен узунунан огу боюнча созулат. Үлгүнүн тартылуу ылдамдыгы туруктуу, жүк атайын сенсор менен өлчөнөт. Ошол эле учурда, узартуу, ошондой эле колдонулган жүккө ылайыктуулугун көзөмөлдөйт. Мындай сыноолордун натыйжалары жаңы конструкциялар жасала турган болсо абдан пайдалуу, анткени алар жүктө кандай иш кыларын азырынча эч ким билбейт. Материалдын ийкемдүүлүгүнүн бардык параметрлерин аныктоо гана сунуш кыла алат. Максималдуу стресс - кирешелүүлүгү берилген материал туруштук бере ала турган максималдуу жүктүн аныктамасын түзөт. Бул коопсуздук чегин эсептөөгө жардам берет.

Катуулук сыноо
Материалдын катуулугу ийкемдүүлүк модулунан эсептелет. Суюктук менен катуулуктун айкалышы материалдын ийкемдүүлүгүн аныктоого жардам берет. Эгерде технологиялык процесс брошинг, прокаттоо, престөө сыяктуу операцияларды камтыса, анда мүмкүн болгон пластикалык деформациянын чоңдугун билүү керек. Жогорку пластикалык менен, материал тиешелүү жүк астында каалаган форманы ала алат. А кысуу сыноо да коопсуздук чегин аныктоо үчүн бир ыкма катары кызмат кыла алат. Өзгөчө материал морт болсо.
Катуулугу колдонуу менен текшерилетБир кыйла катуу материалдан жасалган идентатор. Көбүнчө, бул тест Бринелл методу боюнча жүргүзүлөт (шарты басылган), Викерс (пирамида түрүндөгү идентификатор) же Роквелл (конус колдонулат). Идентификатор материалдын бетине белгилүү бир күч менен белгилүү убакытка чейин басылып, андан кийин үлгүдө калган из изилденет. Башка кеңири колдонулган тесттер бар: соккунун күчү үчүн, мисалы, жүктү колдонуу учурунда материалдын каршылыгы бааланганда.