Тетиктердин жана механизмдердин узак мөөнөткө жана ишенимдүү кызмат кылышы үчүн алар жасалган материалдар керектүү иштөө шарттарына жооп бериши керек. Ошондуктан, алардын негизги механикалык параметрлеринин жол берилген маанилерин көзөмөлдөө үчүн маанилүү болуп саналат. Механикалык касиеттерге катуулук, күч, соккуга каршы күч, ийкемдүүлүк кирет. Металдардын катуулугу негизги структуралык мүнөздөмөсү болуп саналат.
Түшүнүк
Металлдардын жана эритмелердин катуулугу - бул материалдын анын беттик катмарларына башка дене киргенде каршылык көрсөтүү касиети, ал деформацияланбайт жана коштолгон жүктөрдүн (индентер) астында кулабайт. Максаты менен аныкталган:
- алгылыктуу дизайн өзгөчөлүктөрү жана иштөө мүмкүнчүлүктөрү жөнүндө маалымат алуу;
- убакыттын таасири астында абалды талдоо;
- жылуу дарылоонун натыйжаларына мониторинг.
Беттин бекемдиги жана карылыкка туруктуулугу жарым-жартылай ушул көрсөткүчтөн көз каранды. Оригинал катары изилдеңизматериалдык жана даяр бөлүктөрү.
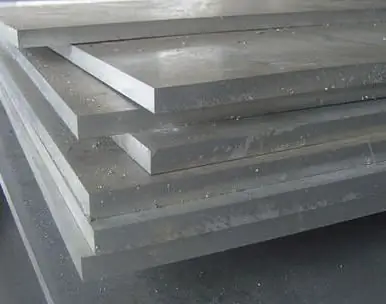
Изилдөө параметрлери
Индикатор катуулук саны деп аталган маани. Металлдардын катуулугун өлчөө үчүн ар кандай ыкмалар бар. Эң так изилдөө - бул эсептөөнүн ар кандай түрлөрүн, интенттерди жана ылайыктуу катуулукту текшерүүчү каражаттарды колдонуу:
- Бринелл: аппараттын маңызы изилденүүчү металлга же эритмеге шарды басып, издин диаметрин эсептөө жана андан кийин механикалык параметрди математикалык эсептөө.
- Роквелл: Топ же алмаз конус колдонулат. Мааниси шкалада көрсөтүлөт же эсептелинет.
- Vickers: Алмаз пирамидасынын учу менен металлдын катуулугун эң так өлчөө.
Бир эле материал үчүн ар кандай өлчөө ыкмаларынын көрсөткүчтөрүнүн ортосундагы параметрдик дал келүүнү аныктоо үчүн атайын формулалар жана таблицалар бар.
Өлчөө опциясын аныктаган факторлор
Лабораториялык шарттарда, жабдуулардын зарыл диапазону менен, изилдөө ыкмасын тандоо даярдалган материалдын айрым өзгөчөлүктөрүнө жараша жүргүзүлөт.
- Механикалык параметрдин индикативдик мааниси. Катуулугу 450-650 НБге чейинки конструкциялык болоттор жана материалдар үчүн Бринелл ыкмасы колдонулат; аспаптык, легирленген болоттор жана башка эритмелер үчүн - Роквелл; катуу эритмелер үчүн - Vickers.
- Сыноо үлгүсүнүн өлчөмдөрү. Өзгөчө кичинекей жана назик бөлүктөрү менен каралатVickers катуулугун текшергичти колдонуу.
- Өлчөө чекитиндеги металлдын калыңдыгы, атап айтканда карбюризацияланган же азоттуу катмар.
Бардык талаптар жана шайкештиктер ГОСТ тарабынан документтештирилген.
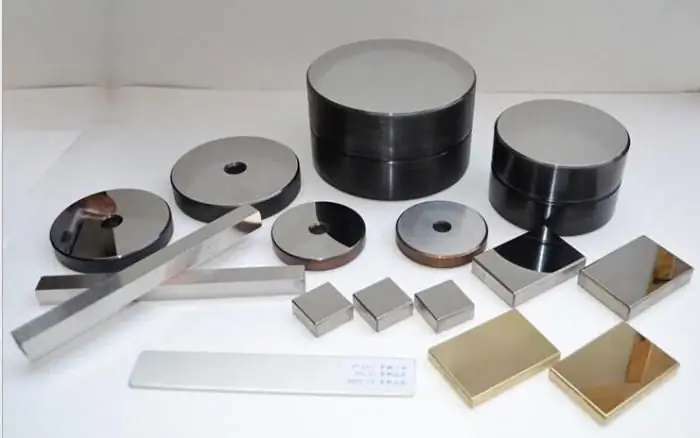
Brinell техникасынын өзгөчөлүктөрү
Металлдардын жана эритмелердин катуулугун Brinell ченегичтин жардамы менен текшерүү төмөнкү өзгөчөлүктөр менен жүргүзүлөт:
- Индентер - диаметри 1, 2, 2, 5, 5 же 10 мм (ГОСТ 3722-81) болгон эритмелүү болоттон же вольфрам карбид эритмесинен жасалган шар.
- Статикалык чегинүүнүн узактыгы: чоюн жана болот үчүн - 10-15 с, түстүү эритмелер үчүн - 30, 60 с узактыгы да мүмкүн, ал эми кээ бир учурларда - 120 жана 180 с.
- Механикалык параметрдин чектик мааниси: болот шар менен ченегенде 450 HB; Карбидди колдонууда 650 HB.
- Мүмкүн жүктөр. Комплектке киргизилген салмактарды колдонуу менен, сыноо үлгүсүндөгү чыныгы деформация күчү оңдолот. Алардын минималдуу жол берилген чоңдуктары: 153, 2, 187, 5, 250 Н; максимум - 9807, 14710, 29420 N (ГОСТ 23677-79).
Формулаларды колдонуу менен, тандалган шариктин диаметрине жана текшерилип жаткан материалга жараша, тиешелүү уруксат берилген чегинүү күчүн эсептөөгө болот.
Эритме түрү | Математикалык жүктөмдү эсептөө |
Болат, никель жана титан эритмелери | 30D2 |
Чойун | 10D2, 30D2 |
Жез жана жез эритмелери | 5D2, 10D2, 30D2 |
Жеңил металлдар жана эритмелер | 2, 5D2, 5D2, 10D2, 15D 2 |
Коргошун, калай | 1D2 |
Белгилөө мисалы:
400HB10/1500/20, мында 400HB металлдын Бринелл катуулугу; 10 - шардын диаметри, 10 мм; 1500 - статикалык жүк, 1500 кгс; 20 - чегинүү мезгили, 20 с.
Так сандарды белгилөө үчүн бир эле үлгүнү бир нече жерден карап чыгып, алынгандардын орточо санын табуу менен жалпы жыйынтыкты аныктоо рационалдуу.
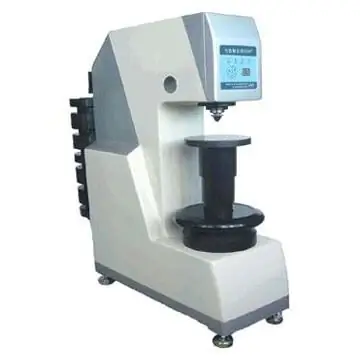
Бринелл катуулугун сыноо
Изилдөө процесси төмөнкү ырааттуулукта жүрөт:
- Белтиктин талаптарга ылайык келишин текшерүү (ГОСТ 9012-59, ГОСТ 2789).
- Түзмөктүн ден соолугу текшерилүүдө.
- Керектүү топту тандоо, мүмкүн болгон күчтү аныктоо, аны түзүү үчүн салмактарды коюу, чегинүү мезгили.
- Катуулугун текшергичти ишке киргизүү жана үлгүнүн деформациясы.
- Терешиктин диаметрин өлчөө.
- Эмпирикалык эсептөө.
НВ=F/A, мында F - жүк, kgf же N; A - басып чыгаруу аянты, mm2.
НВ=(0, 102F)/(πDh), мында D - шардын диаметри, мм; h - басып чыгаруу тереңдиги, мм.
Бул ыкма менен өлчөнгөн металлдардын катуулугу менен эмпирикалык байланыш баркүч параметрлерин эсептөө. Бул ыкма так, өзгөчө жумшак эритмелер үчүн. Бул механикалык касиеттин баалуулуктарын аныктоо тутумдарында негизги болуп саналат.
Роквелл техникасынын өзгөчөлүктөрү
Өлчөөнүн бул ыкмасы XX кылымдын 20-жылдарында ойлоп табылган, мурункуга караганда автоматташтырылган. Катуураак материалдар үчүн колдонулат. Анын негизги мүнөздөмөлөрү (ГОСТ 9013-59; ГОСТ 23677-79):
- 10 кгс негизги жүктүн болушу.
- Катуу мөөнөтү: 10-60 с.
- Мүмкүн болгон көрсөткүчтөрдүн чектик маанилери: HRA: 20-88; HRB: 20-100; HRC: 20-70.
- Сан катуулукту текшергичтин циферблатында көрсөтүлгөн, аны арифметикалык түрдө да эсептесе болот.
- Таразалар жана интентерлер. Индентер түрүнө жана максималдуу жол берилген статикалык жүккө жараша 11 түрдүү тараза бар. Көбүнчө колдонулат: A, B жана C.
A: Алмаз конусу учу, 120˚ чекит бурч, 60кг жалпы статикалык күч, HRA; жука продуктулар, негизинен прокаттар изилденет.
C: ошондой эле 150kgf HRC алмаз конус, катуу жана катууланган материалдарга ылайыктуу.
B: катууланган болоттон же катуу вольфрам карбидинен жасалган 1,588 мм шар, жүк 100 кгс, HRB, күйдүрүлгөн азыктардын катуулугун баалоо үчүн колдонулат.
Топ формасындагы учу (1,588 мм) Rockwell B, F, G таразалары үчүн жарактуу. Ошондой эле E, H, K шкалалары бар, алар үчүн диаметри 3,175 мм болгон шар (ГОСТ 9013-59) колдонулат.
Үлгүлөрдүн саны,бир аймакта Rockwell катуулугун текшерүүчү менен жасалган бөлүгүнүн өлчөмү менен чектелген. Экинчи сыноого мурунку деформация болгон жерден 3-4 диаметр аралыкта жол берилет. Сыналган буюмдун калыңдыгы да жөнгө салынат. Ал учтун кирүү тереңдигинен 10 эсе кем болбошу керек.
Белгилөө мисалы:
50HRC - Роквеллдин металлдын катуулугу, алмаздын учу менен өлчөнгөн, анын саны 50.
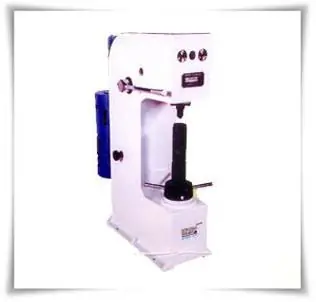
Роквеллди изилдөө планы
Металлдын катуулугун өлчөө Бринелл ыкмасына караганда жөнөкөйлөштүрүлгөн.
- Белтиктин өлчөмдөрүн жана беттик мүнөздөмөлөрүн баалоо.
- Түзмөктүн ден соолугу текшерилүүдө.
- Учунун түрүн жана жүктөө сыйымдуулугун аныктаңыз.
- Үлгүн коюу.
- Материалга негизги күчтүн ишке ашырылышы, 10 кгс мааниси.
- Толук жана туура аракет кылуу.
- Алынган номерди терүүнүн шкаласы боюнча окуу.
Механикалык параметрди так аныктоо үчүн математикалык эсептөө да мүмкүн.
60 же 150 кгс жүгү бар алмаз конусун колдонгондо:
HR=100-((H-h)/0, 002;
100 кгс күч астында шар менен сыноодо:
HR=130-((H-h)/0, 002, мында h - 10 кгс негизги күчтө интентердин өтүү тереңдиги; H - толук жүктөөдө интентердин өтүү тереңдиги; 0, 002 - катуулук саны 1 бирдикке өзгөргөндө учтун кыймылынын көлөмүн жөнгө салуучу коэффициент.
Роквеллдин ыкмасы жөнөкөй, бирок жетиштүү так эмес. Ошол эле учурда ал катуу металлдардын жана эритмелердин механикалык касиеттерин өлчөй алат.
Викерс техникасынын өзгөчөлүктөрү
Бул ыкма менен металлдардын катуулугун аныктоо эң жөнөкөй жана так. Катуулукту текшергичтин иши үлгүдөгү алмаз пирамидасынын учу чегинүүгө негизделген.
Негизги өзгөчөлүктөрү:
- Индентер: 136° чокусу алмаз пирамидасы.
- Уруксат берилген максималдуу жүк: легирленген чоюн жана болот үчүн - 5-100 кгс; жез эритмелери үчүн - 2,5-50 кгс; алюминий жана анын негизиндеги эритмелер үчүн - 1-100 кгс.
- Статикалык жүктү кармоо мөөнөтү: 10-15 с.
- Сыналган материалдар: катуулугу 450-500 HB жогору болот жана түстүү металлдар, анын ичинде химиялык термикалык иштетүүдөн кийинки продукциялар.
Белгилөө мисалы:
700HV20/15, мында 700HV - Викерс катуулугунун саны; 20 - жүк, 20 кгс; 15 - статикалык аракет мезгили, 15 с.
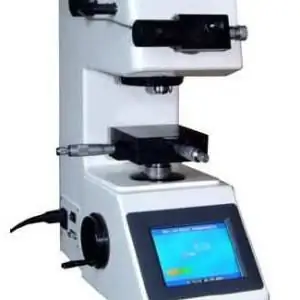
Виккерс изилдөө ырааттуулугу
Процедура өтө жөнөкөйлөштүрүлгөн.
- Үлгү менен приборлорду текшерүү. Тетиктин бетине өзгөчө көңүл бурулат.
- Уруксат берилген аракетти тандоо.
- Сыноо материалы орнотулууда.
- Катуулукту текшергич ишке киргизилүүдө.
- Натыйжаны терүүдөн окуңуз.
Бул ыкма менен математикалык эсептөө төмөнкүдөй:
HV=1, 8544(F/d2), бул жерде F - жүк,кгф; d - басып чыгаруу диагоналдарынын узундуктарынын орточо мааниси, мм.
Бул металлдардын, жука жана майда тетиктердин катуулугун өлчөөгө мүмкүндүк берет, ошол эле учурда натыйжанын жогорку тактыгын камсыздайт.
Таразалар ортосундагы өтүү ыкмалары
Атайын жабдыктын жардамы менен басып чыгаруунун диаметрин аныктагандан кийин, сиз таблицаларды колдонуп катуулугун аныктай аласыз. Металлдардын катуулук таблицасы бул механикалык параметрди эсептөөдө далилденген жардамчы болуп саналат. Демек, эгер Бринеллдин мааниси белгилүү болсо, тиешелүү Викерс же Роквелл санын оңой аныктоого болот.
Кээ бир дал келген маанилердин мисалы:
Басып чыгаруу диаметри, мм | Изилдөө ыкмасы | ||||
Бринелл | Роквелл | Виккерлер | |||
A | C | B | |||
3, 90 | 241 | 62, 8 | 24, 0 | 99, 8 | 242 |
4, 09 | 218 | 60, 8 | 20, 3 | 96, 7 | 218 |
4, 20 | 206 | 59, 6 | 17, 9 | 94, 6 | 206 |
4, 99 | 143 | 49, 8 | - | 77, 6 | 143 |
Металлдардын катуулугунун таблицасы эксперименталдык маалыматтардын негизинде түзүлгөн жана жогорку тактыкка ээ. Бринеллдин катуулугунун темир-көмүртек эритмесиндеги көмүртектин курамына графикалык көз карандылыгы да бар. Ошентип, мындай көз карандылыкка ылайык, курамында көмүртектин көлөмү 0,2% болгон болот үчүн бул 130 HB.
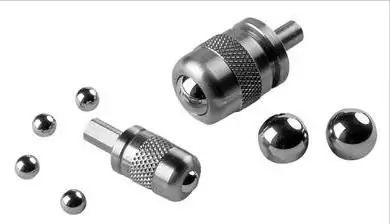
Үлгү талаптары
ГОСТтун талаптарына ылайык, сыналган тетиктер төмөнкү мүнөздөмөлөргө жооп бериши керек:
- Даярдоо тегиз болушу керек, катуулугун текшергичтин үстөлүнө бекем жатышы керек, анын четтери жылмакай же кылдаттык менен иштетилиши керек.
- Беттин эң аз бүдүрлүү болушу керек. кумдап жана химиялык кошулмалардын жардамы менен, анын ичинде тазалоо керек. Ошол эле учурда механикалык иштетүү процесстеринде жумуштун катууланышынын пайда болушуна жана иштетилген катмардын температурасынын жогорулашына жол бербөө маанилүү.
- Бөлүк параметрдик касиеттери боюнча катуулукту аныктоо үчүн тандалган ыкмага ылайык келиши керек.
Негизги талаптарды аткаруу так өлчөө үчүн милдеттүү шарт болуп саналат.
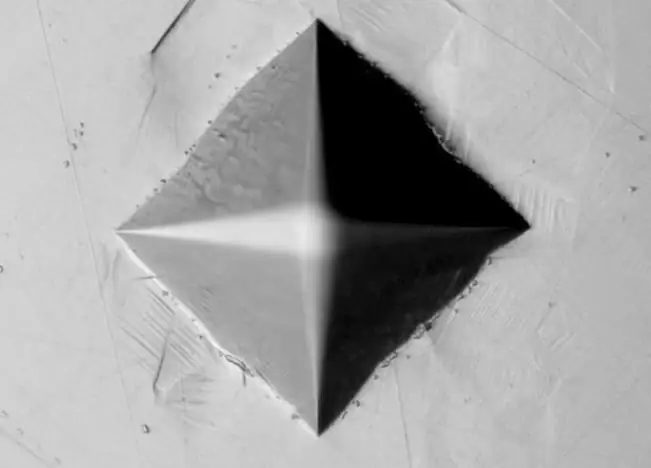
Металлдардын катуулугу алардын кээ бир башка механикалык жана технологиялык өзгөчөлүктөрүн, мурунку иштетүү процесстеринин натыйжаларын, убакыт факторлорунун таасирин жана мүмкүн болгон иштөө шарттарын аныктоочу маанилүү фундаменталдык механикалык касиет болуп саналат. Изилдөөнүн методологиясын тандоо тандоонун болжолдуу мүнөздөмөлөрүнө, анынпараметрлери жана химиялык курамы.